
Bending & Forming Services

​Whether you need brackets, panels, or custom-formed components, our advanced bending equipment ensures clean, accurate bends with consistent results. Perfect for fabrication, manufacturing, and custom projects, we deliver high-quality formed parts with quick turnaround times. Contact us today to get started!
​
-
Maximum bending thickness 1/4" - for larger applications
-
Available with mild steel, stainless steel & aluminum
-
Bending services can sometimes impact lead times
Benefits of bending
Metal bending offers a cost-effective and precise way to shape sheet metal without the need for welding or additional fasteners. This process improves structural integrity, reduces assembly time, and enhances durability by creating smooth, seamless bends. Ideal for brackets, enclosures, frames, and custom components, bending ensures stronger, lightweight designs with a clean, professional finish.


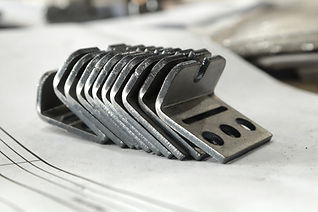
Key Considerations When Designing Forming and Bending Components
​Designing sheet metal parts for bending and forming requires careful planning to ensure precision, manufacturability, and cost-effectiveness. We work with designers and engineers to create parts that meet both functional and aesthetic requirements while optimizing for efficient fabrication. Here are some essential factors to consider when designing metal components for bending and forming.
​
​
Material Selection
​
The type of metal you choose impacts bending behavior, strength, and overall manufacturability. Some key factors include:
-
Ductility & Formability – Materials like aluminum and mild steel bend easily, while stainless steel and high-strength alloys may require specialized tooling.
-
Thickness – Thicker metals require more bending force and may have greater springback.
-
Grain Direction – Bending perpendicular to the grain structure reduces the risk of cracking and material failure.
​
​
Bend Radius
​
The inside bend radius is a critical factor in designing formed components. Key considerations:
-
The minimum bend radius should be at least equal to the material thickness to avoid cracking.
-
A larger bend radius reduces stress concentration and improves part longevity.
-
Consistent bend radii across a design simplify production and reduce tooling costs.
​
​
Bend Allowance & K-Factor
​
When metal bends, the material stretches on the outside and compresses on the inside. To ensure accurate dimensions, consider:
-
Bend Allowance – The amount of material needed to accommodate bending without distorting final part dimensions.
-
K-Factor – A material-specific value that determines how much stretching occurs in the bend zone.
-
Neutral Axis Shift – The center of the material thickness shifts during bending, affecting flat pattern layouts.
Proper calculations prevent errors in cut length and ensure components fit as intended.
​
​
Avoiding Common Bending Defects
​
Designing with manufacturability in mind can prevent issues such as:
-
Springback – Metals like stainless steel tend to return slightly to their original shape after bending. Compensation techniques include overbending or coining.
-
Cracking or Fracturing – Occurs when bend radii are too small or grain direction isn’t considered.
-
Wrinkling or Distortion – Can happen with large unsupported sections or improper bend sequencing.
​
​
Hole & Cutout Placement
​
If a design includes holes, cutouts, or notches near bends, they must be positioned correctly to avoid deformation:
-
Keep holes at least 1.5 times the material thickness away from the bend line.
-
For slots or large cutouts, reinforcement or alternative placement may be required.
-
If holes must be placed near bends, pre-bending relief cuts can help maintain accuracy.
​
​
Tolerances & Manufacturing Constraints
​
Laser cutting, waterjet cutting, and bending all have inherent tolerances that should be accounted for in the design:
-
Bending tolerances vary depending on material type, thickness, and machine precision.
-
Overly tight tolerances increase costs due to additional setup and machining time.
-
Consider GD&T (Geometric Dimensioning and Tolerancing) to ensure proper fit and function.
​
​
Bend Sequencing & Design for Assembly
​
-
Minimize the number of bends to reduce complexity and production costs.
-
Plan for easy assembly – Tabs, slots, or self-locating features can simplify part alignment.
-
Avoid over-constraining – Overlapping bends may require special tooling or multi-step forming processes.
​
​
Cost Considerations & Efficiency
​
-
Standardize bend angles and radii to reduce custom tooling costs.
-
Minimize secondary operations like welding, grinding, or finishing by designing efficient bend sequences.
-
Optimize sheet utilization – Nesting parts effectively minimizes waste and material costs.
​
​
Conclusion
​
By following these design best practices, you can create stronger, more cost-effective, and manufacturable sheet metal components. At CadCutShip, we work closely with clients to optimize designs for bending and forming, ensuring precision and efficiency in every project.
​​
​
If you need assistance with your metal forming project, contact us today to discuss your requirements and get expert guidance!
FAQ: What is sheet metal K-Factor?
The K-factor in sheet metal bending is a ratio that determines how the material stretches and compresses during bending. It represents the neutral axis shift, which is the point in the material that doesn’t stretch or compress.
​
What You Should Know When Designing Parts:
-
K-Factor Affects Bend Allowance – It helps calculate how much material is needed to achieve the correct final dimensions after bending.
-
Material & Thickness Matter – Different metals and thicknesses have different K-factors. Softer metals like aluminum stretch more than steel.
-
Smaller Bends = More Compression – A tighter bend radius means more material compression and stretching, affecting accuracy.
-
Consistent K-Factor = Better Fit – Using the correct K-factor ensures your flat patterns bend correctly and fit as expected.